Grade
At rest
In operation
0.5 pe
5.5 m
0.5 pe
5.5
A
3520
20
3520
20
B
3520
29
352,000
2900
C
352,000
2900
3,520,000
29,000
D
3,520,000
29,000
Not defined
Not defined
A conventional PET radiopharmaceutical production room in a university lab or research hospital usually has multiple hotcells enclosing various synthesis modules. Each module is connected by a dedicated fluid transfer tube that transports a formulated product to a distant hotcell for dispensing and packaging [5, 6]. This dispensing space is responsible for handling multiple incoming formulated products from different synthesizers. Aseptic filtration of formulated products is usually performed in this hotcell as well. This type of space is not too difficult to be transformed into a cleanliness-controlled complex according to the above guidance, as long as the dispensing hotcell can be kept in a Grade A room, which is located at Grade B environment, although this is only from the viewpoint of cleanroom grading (Fig. 3.1). There are many other designs that might better suit various purposes in PET radiopharmaceutical production. As an example, this section describes a new concept in an industrial PET radiopharmaceutical manufacture facility. This site is a centralized PET radiopharmaceutical provider in Taiwan, and it has been certified according to PIC/S GMP guide by the Taiwanese authority (Fig. 3.2).
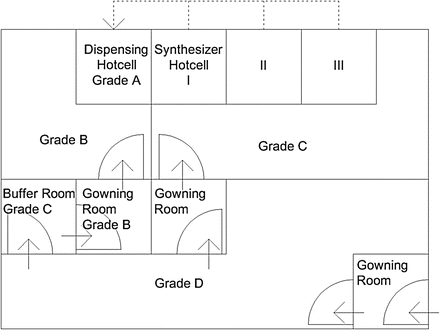
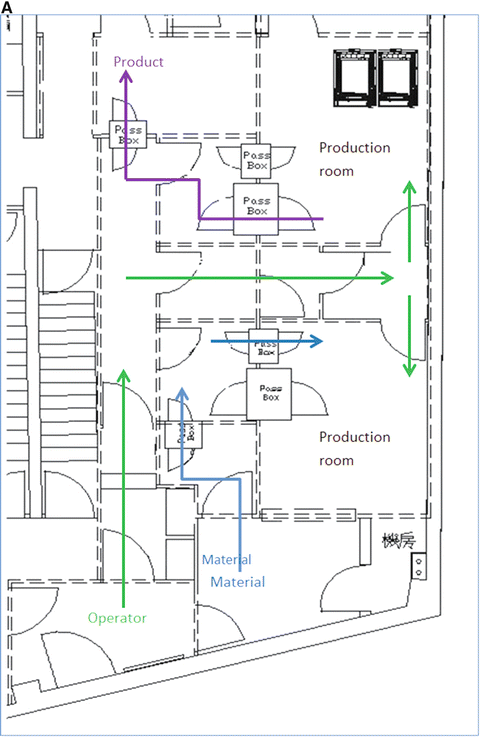
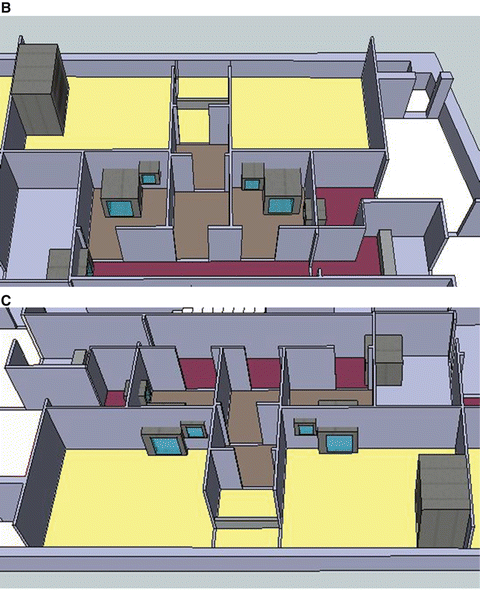
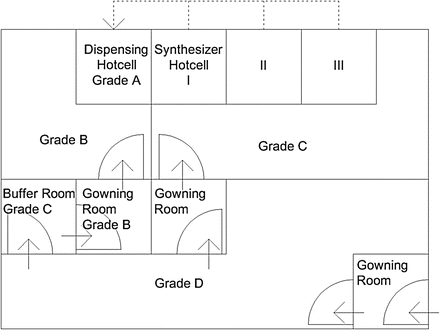
Fig. 3.1
This is a conceptual drawing of a conventional PET radiopharmaceutical production complex that follows basic cleanroom requirement of PIC/S GMP guidance. A row of three hotcells for synthesizers is in a Grade C room, while a Grade A dispensing hotcell is in a separate Grade B room. Dotted lines indicate transport tubes from each synthesizer. This drawing does not depict necessary functions such as pass boxes for material in and product out
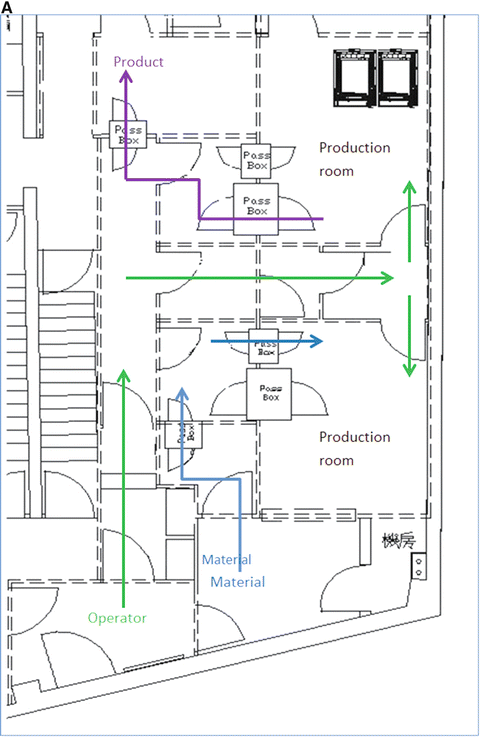
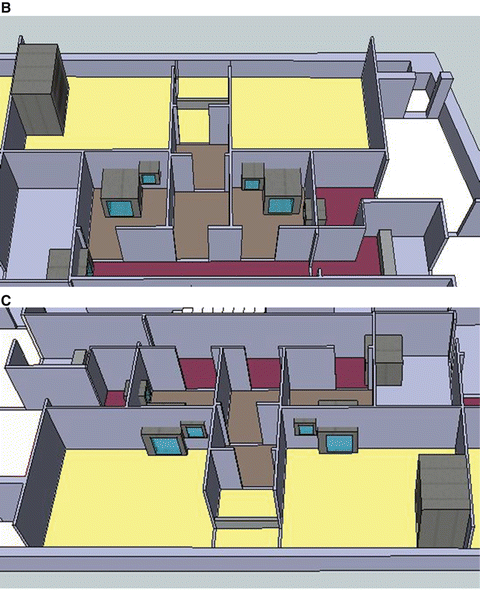
Fig. 3.2
This is the actual cleanroom complex in PET Pharm Biotech Co Ltd. (a) Floor plan. Operators enter through left bottom corner (green arrow) into a Grade D corridor. The two production rooms are assessed via series of small buffer spaces. Only the upper production room is depicted with a hotcell in this drawing. (b) 3D rendition of the floor viewing from the left side of the plan. Crimson color floor is Grade D while gray C and yellow B. The final gowning and two production rooms are in Grade B. Two rooms with pass boxes in Grade C are for passing of materials and products. (c) Viewing from the opposite angle
This alternative design argued that multiple small Grade B rooms, each setup with a hotcell encasing one Grade B synthesis compartment and one Grade A aseptic filling compartment, would be a more efficient way for complying the toughest GMP, especially in a site that more than one kind of PET radiopharmaceuticals are regularly produced and dispensed.
Entering via a series of small rooms that increase in the cleanliness grades, the Grade B final gowning room opens to two Grade B production rooms. In each production room (12 m2) stands one hotcell with two main compartments. The synthesis compartment is not controlled for its air particles to a specific standard, but because it opens to the production room, and thus it is in the same level of cleanliness as the production room itself. The other compartment of the hotcell is for aseptic filling; it is therefore designed to be an isolator of Grade A. Inside this isolator, particle counts are monitored continuously and air is sampled for bacteria.
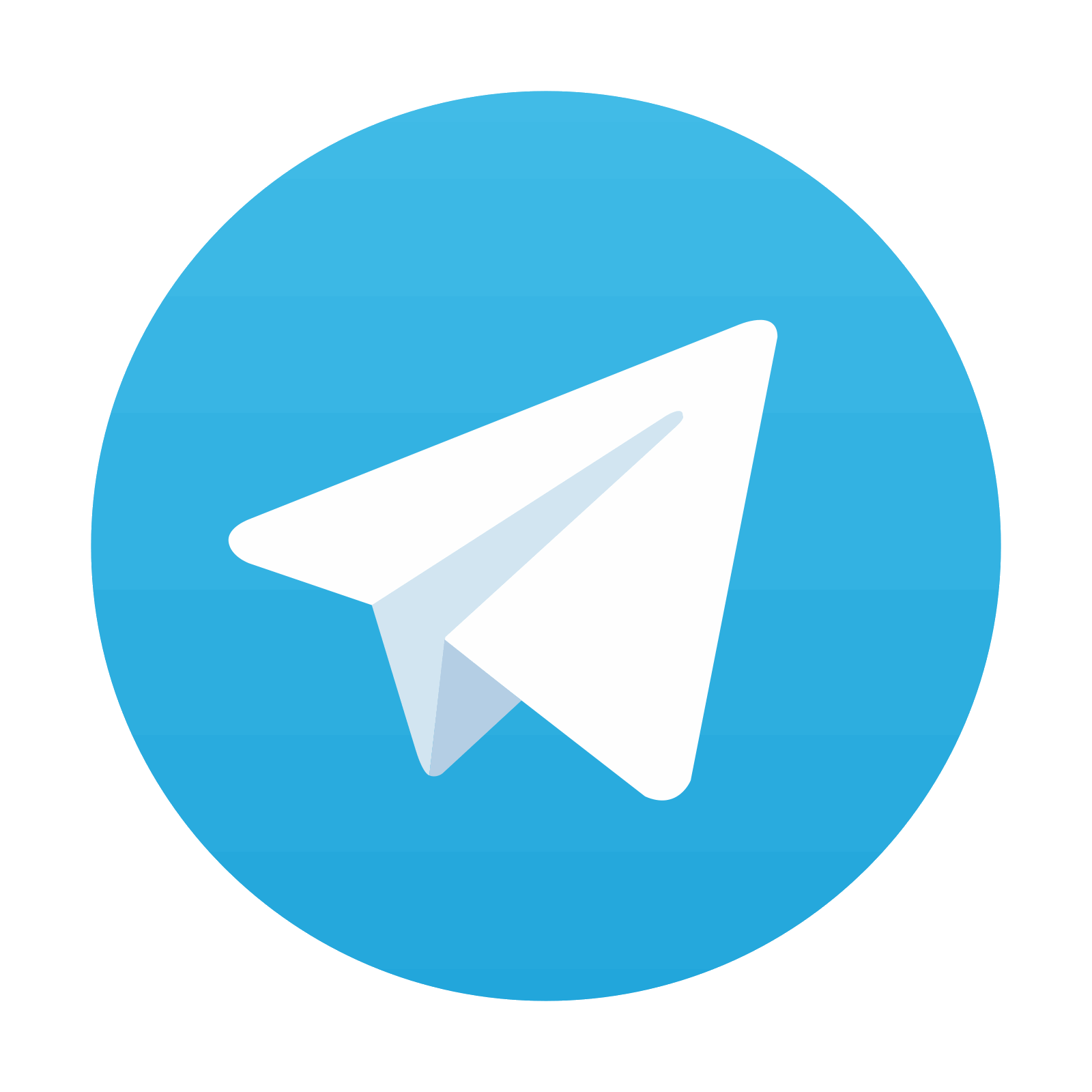
Stay updated, free articles. Join our Telegram channel
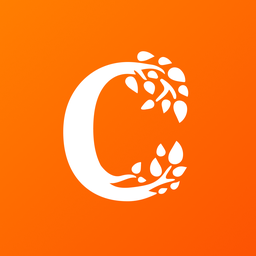
Full access? Get Clinical Tree
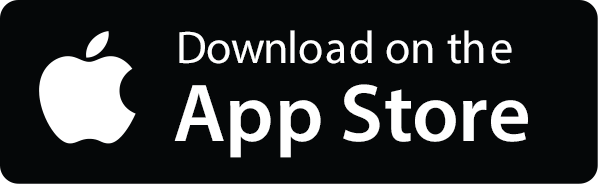
